Что такое пресс-форма?
Пресс-форма — это сложный по конструкции технологический инструмент для производства изделий из пластмасс, которое задает конфигурацию изделия при литье под давлением.
Литьевая форма определяет параметры будущей отливки, от первичных: длина, ширина, высота, и до вторичных: шероховатость и фактура поверхности, плотность изделия (плотность напрямую связана с прочностью). Этот инструмент — главное звено в серийном и массовом производстве деталей из пластика и других материалов.
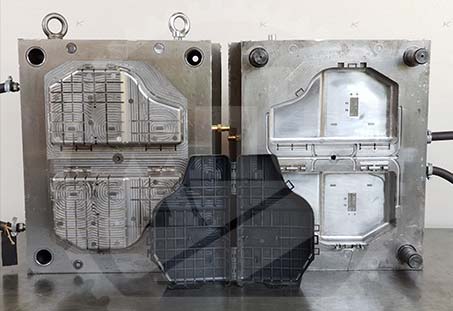
Этапы производства пресс-форм.
Изготовление проходит этапы – от проектирования до испытаний формы на работоспособность.
Дизайн изделия
Первый этап определяет необходимый объем работ. Перед проектированием формы конструктор должен понимать, как будет выглядеть отливка, для этого, предварительно, делают наброски готового изделия.
На основе этих эскизов проектируется 3D-модель отливки, количество изделий в литьевом механизме, производится расчет поперечного сечения литников, размеров формообразующих деталей (матрицы, пуансона, знаков), расчет усадки изделия.
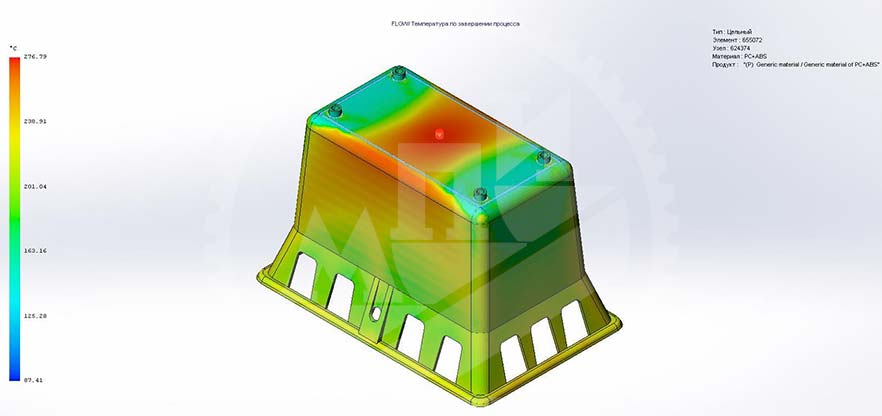
На данном этапе появляется возможность выявить погрешности, устранив дефекты, неточности. Модель изделия проходит проверку по нескольким параметрам методом конечно-элементного анализа. Результаты анализов дают рекомендации, где лучше всего выбрать точку впрыска, определяет кривизну поверхности, равномерность толщины стенок, скругления, уклоны.
Проектирование пресс-формы
На втором этапе рождается 3D- модель непосредственно пресс-формы и конструкторская документация. Эта стадия определяет необходимый набор стандартных изделий, составных частей и компонентов литьевой оснастки. Все элементы составляющей должны быть точно подобраны друг к другу.
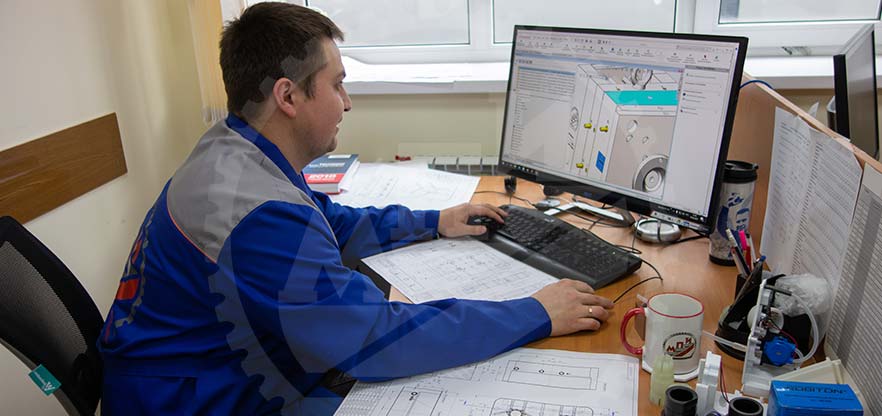
Этап изготовления пресс-формы
Значительная часть всех составляющих элементов литьевой оснастки проходит обработку на оборудовании с ЧПУ и электроэрозионных станках. Предполагается следующая технология обработки:
- ■Стандартный пакет плит (корпусные детали пресс-формы) обрабатывается, в одну стадию на фрезерных станках с ЧПУ.
- ■Формообразующие детали (пуансон, матрица) обрабатываются в следующем порядке:
- Черновая механическая обработка, при которой снимается основное слой материала, назначаются припуски на рабочие поверхности от 0,5 до 1,5мм.
- Термическая обработка в вакуумной печи, которая предполагает закалку формообразующих деталей, создавая износостойкость рабочих поверхностей.
- Получистовая и чистовая обработка – значимая часть, на которой выполняются точная обработка рабочих поверхностей. Если в отливке преобладают тонкостенные ребра, поднутрения, острые, прямые углы, то пуансон с матрицей проходят обработку дополнительно на электроэрозионных станках.
- Финишная доводка и отделка рабочих поверхностей может включать в себя различные методы – от ручной полировки до электрохимической и лазерной обработки.
- При необходимости на формообразующие поверхности наносятся различные покрытия и выполняется поверхностное упрочнение.
Сборка и испытание.
Для подгонки и сборки пресс-форма переходит в руки слесаря-инструментальщика, так как для надежной работы механизма необходима тщательная пригонка всех его частей. Именно на этой стадии обнаруживаются недоработки, исправляются все ошибки.
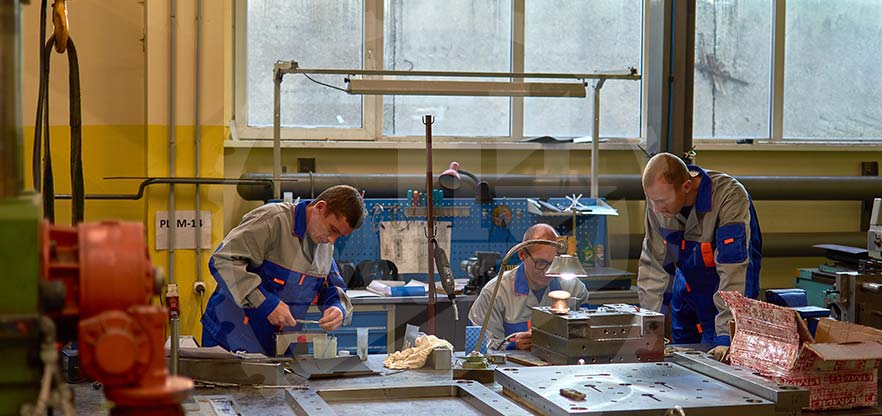
Каждая пресс-форма индивидуальна, поэтому сборка – ответственный момент, который может затянуться, пока не будут выполнены все требования по геометрии формующих поверхностей и работы механизмов пресс-формы, согласно чертежу
Все этапы преследуют одну цель – получение литьевой оснастки заданного качества. Поэтому испытания проводятся в реальных условиях эксплуатации.
Если во время испытаний выявились недочеты, то группа инженеров мгновенно принимает решение о доработке, при необходимости – связывается с заказчиком.
Устройство пресс-формы.
Итак, подытожим, что литьевая оснастка – это конструкция для создания серийного количества однотипных изделий конкретной геометрии и стабильного качества, подробнее смотрите тут. Из чего же она состоит?
Основными узлами являются:
Пакет плит (корпус пресс-формы)
В общем случае он состоит: верхние и нижние плиты крепления, брусья, обойма матрицы, обойма пуансона, плита толкателей, плита хвостовика. В зависимости от типа и сложности формы состав пакета может изменяться.
Формообразующие детали (ФОД)
Это детали, которые при закрытии пресс-формы образуют полость, в которую заливается пластмасса. К ФОД относятся, как правило, следующие детали:Пуансон – основной элемент ФОД, расположен на подвижной части пресс-формы.Матрица — основной элемент ФОД, расположена на неподвижной части пресс-формы.Ползуны – детали, движение которых происходит в плоскости перпендикулярной направлению смыкания или размыкания пресс-формы и имеют отдельный привод. Привод может быть как от движения раскрытия или закрытия пресс-формы, так и внешним (гидравлическим, пневматическим и т.д.) Ползуны вводятся в конструкцию пресс-формы при необходимости сформировать сложные боковые поверхности отливки.Знаки как правило, съемные элементы ФОД, служат для оформления отверстий, карманов, пазов, поднутрений и т.п. Знаки бывают подвижными и неподвижными. Также сменные знаки могут применятся для выпуска разных, но схожих по геометрии деталей на одной пресс-форме.
Следует упомянуть так называемые закладные знаки. Они применяются для опытных и малосерийных пресс-форм. Закладной знак представляет из себя элемент ФОД, который устанавливается в пресс-форму перед каждым циклом литья, извлекается из пресс-формы вместе с отливкой, извлекается из отливки и устанавливается обратно в пресс-форму.
Для выполнения внутренней резьбы применяются вращающиеся знаки, они могут иметь механический, гидравлический или электрический привод. Для выполнения резьбы в недорогих вариантах изготовления пресс-форм используются закладные резьбовые знаки, они выкручиваются из отливки оператором и устанавливаются в пресс-форму вручную. В таком случае изготавливается несколько комплектов закладных знаков. Этот вариант не подходит для воспроизводительной работы, т.к. ТПА работает только в режиме Полуавтомат.
Элементы ФОД могут быть как цельными деталями, так и сборными узлами. Конкретное исполнение ФОД зависит от геометрии отливки, технических требований к пресс-форме и технологических возможностей изготовителя.